Here’s a bulletproof window secret: most bulletproof barrier installers have next to no experience with bulletproof materials. This is because most bulletproofing companies have chosen a niche and specialize in it. They have one product where they truly excel—maybe custom doors, or certain window styles, or a specific type of client. For the rest, they are reselling third-party products or outsourcing the actual work to contractors. In almost every case, that means relying on a “network” of independent installers.
“Different companies are adept at different things,” says Total Security Solutions CEO Jim Richards. “But the installation is one of the harder parts. It’s just one of those inglorious positions because a lot of things can go wrong. Think about your cable installer. Is anyone ever happy with him? As a result, I think most companies do everything they can to have no part in the installation.”
In theory, it should make little difference who installs the system. After all, that is what contractors do: They install components designed, engineered, and fabricated elsewhere.
For a good contractor, hanging a door or installing a window is a little more complicated than building with LEGOs. But bulletproof barrier systems are fundamentally different from a non-bullet-resistant door or window. Bulletproof windows and doors need to seamlessly mesh with the building. Even a “standard” system will need some custom fabrication. Most companies are relying on one-off manual processes. As a result, a modern bulletproof barrier can be a precision hand-made jigsaw puzzle. People who do a lot of puzzles are great at doing puzzles. But very few general contractors are called upon to do this work enough to be confident with it. That can simply lead to an ugly installation. But it can also mean more.
Why Installation Quality Matters
This isn’t just about aesthetics. All too often, an ugly installation is also a fundamentally bad one. For example, consider something Jim’s install crews have actually seen out in the world: bullet-resistant barriers installed entirely backward. In one case, they found a situation where previous installers had reversed a baffle system.
Baffle systems are very popular in corporate and municipal offices. Here’s a good example of a baffle-style bulletproof window system:
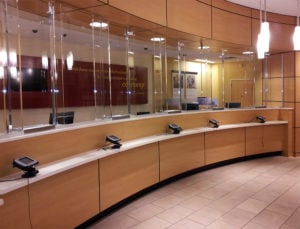
baffle-style bulletproof windows
As you can see in this detail, in a baffle barrier the primary protection is a single unbroken piece of ballistic acrylic. It stands directly in front of the staff member and is offset behind the rest of the barrier system:
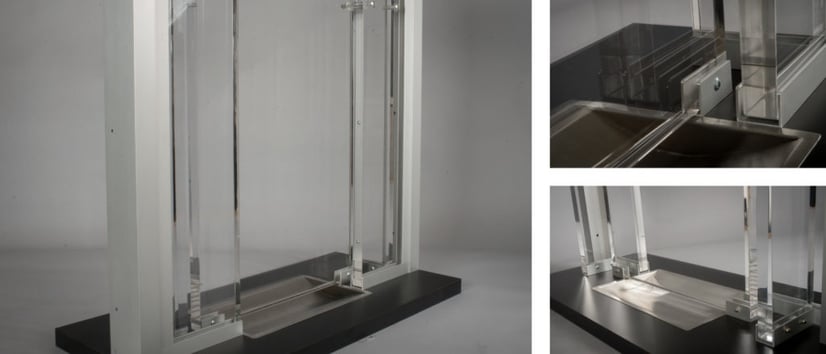
a closer loom at baffle window components
When contractors install such a system backward, that primary protection is offset toward the customer, in front of the rest of the barrier. The result isn’t just awkward looking. In such a configuration, an armed assailant can angle their gun into the gap around the baffle and successfully fire into occupied areas of the “secure area”.
Setting safety aside, having the baffles reversed like this undermines every other aspect of the barrier’s performance on a daily basis. It’s harder to hear through (arranging the acrylic like this bounces voices into the partition, muffling them). And it can badly disrupt airflow, straining HVAC systems, and wreaking havoc with indoor air quality (and thus both the staff and visitor experience).
How to Evaluate a Bulletproof Window Installation
Trevor Smith is an operations analyst for TSS, where he oversees installations. Instead of niching in product or service, TSS has elected to expand their installation crews both in size and experience. Today TSS has the largest—and most sought after—bulletproof glass installation team in North America. According to Trevor, the quality of an installation is a good indicator of the thought and care that went into the entire production process. “Knowing the products and materials, understanding how they are fabricated from the very first step is really vital to knowing what can and can’t be done, and what the outcomes will be like.”
He urges everyone to take a good look at the quality of a company’s installations before deciding to work with them. Hallmarks of a good installation include tightly aligned frames, clean caulk joints, and components coming together smoothly (no odd gaps, inconsistent finishes, or rough edges).
Look for little details: Are the clips holding the bulletproof glass in place high-quality? Do they fit snugly? Did the installers scratch the glass when they were sliding them into place?
Any company will flame polish or otherwise finish the exposed edges of a piece of bullet-resistant acrylic glass. A top-notch company will flame polish every edge, even those that will be mostly concealed by channel or trim.
Visible signs of a poor installation process demonstrate the install team’s underlying lack of materials knowledge and problem-solving capabilities. That, in turn, has a meaningful, lasting impact on the barrier’s durability, daily functionality, and value.
(Total Security Solutions CEO Jim Richards offers more advice on developing a keen eye for a bulletproof window installation here: “Ballistic Glass: 7 Common Install Mistakes“)
A Commitment to Flawless Installation
In Trevor’s experience, this is the major advantage to working with a company that handles an entire job, from the earliest design and engineering steps, through the installation.
This is especially the case in retrofits and renovations, where it can be very challenging for specialists to “figure out how the barrier interacts with what’s already there. People without experience with the materials don’t understand. In contrast to most construction situations, it’s hard—if not impossible—to fabricate this stuff in the field. If the measurement is off, the engineering is going to be off, and then the whole barrier doesn’t work.”
As an example, Trevor points to what happens very often when a general contractor goes out to measure the radius of a curved desk for a barrier during the project planning stages.
So often, those measurements are all wrong. A lot of people just don’t understand how to measure a radius, or how a [bulletproof window] system interacts with the radius itself. They don’t know where to start, where to end, or what measurement the fabricator producing that system needs. The end result is a system that doesn’t work, or works but doesn’t fit, or only fits because the contractor cut more holes and went over schedule and budget to make it fit.
As TSS CEO Jim Richards explains:
“I think what separates us is that we’re adept at all parts of the installation. We can be glaziers, we can be door guys, we can be millworkers. We have really well-rounded crews. I don’t know if you necessarily get that with other companies, because it doesn’t happen by accident. You have to make part of your focus having a well-rounded crew that can adapt and find solutions.”